430 Stainless Steel Oscillating Band: SSBANDING’s Cost-Effective Solution for Automated Production Lines
Description:
As a leading China 430 stainless steel oscillating band supplier, SSBANDING combines chromium-rich ferritic alloys with patented oscillation processing to deliver 20% productivity gains. Explore our burr-free edge technology and sustainable manufacturing.
Table of Contents
Introduction: The Rise of 430 Stainless Steel in Smart Manufacturing
In the era of Industry 4.0, 430 stainless steel oscillating bands have emerged as a game-changer for cost-sensitive automated systems. SSBANDING, China’s pioneer in ferritic stainless steel processing, leverages chromium-rich alloys (16-18% Cr) and proprietary oscillation technologies to create coils that outperform traditional materials in durability, magnetic compatibility, and operational efficiency.
This article decodes the science behind SSBANDING’s 430 oscillating bands, from metallurgical advantages to production breakthroughs, and why global manufacturers are transitioning from 304-grade steel to this innovative solution.
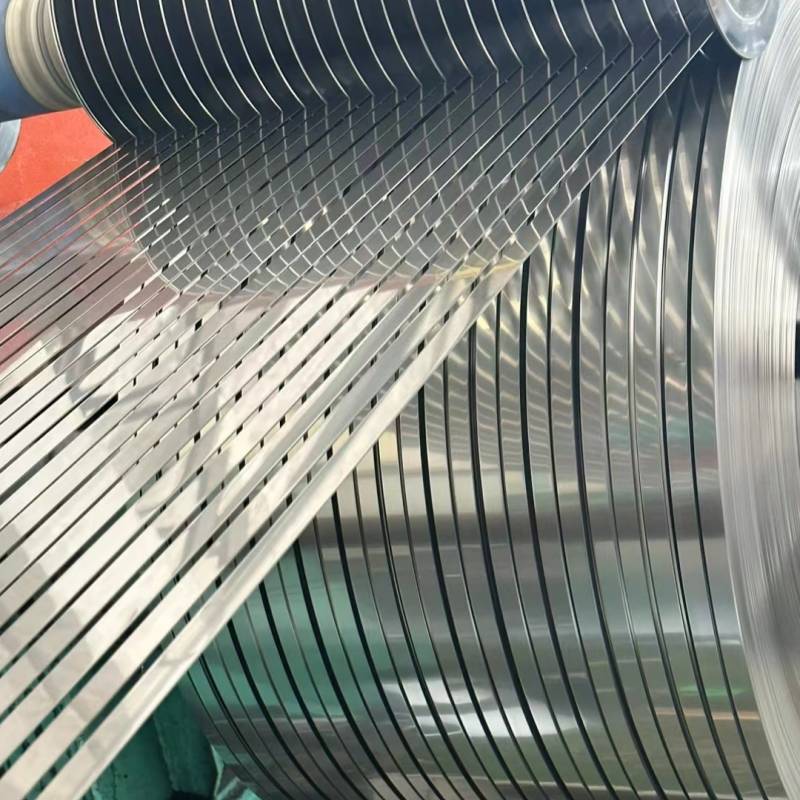
Chapter 1: Why 430 Stainless Steel? Material Superiority & Naming Logic
Technical Definition of “Oscillating Band”
The term “oscillating band” originates from its dynamic movement pattern in automated feeding systems. Unlike static coils, SSBANDING’s welded oscillating coils utilize controlled back-and-forth motion (oscillation) during unwinding, achieving:
- 95% reduction in material reloading frequency
- Zero line-jamming via tension-optimized oscillation slitting
- Magnetic compatibility for robotic grippers in automotive assembly
Metallurgical Advantages of Grade 430
SSBANDING’s 430 stainless steel oscillating bands excel with:
- Chromium-rich matrix: 16-18% Cr content ensures oxidation resistance in temperatures up to 850°C
- Cost efficiency: Nickel-free composition cuts material costs by 30-40% vs. 304-grade
- Magnetic permeability: Ideal for sensor-integrated production lines (μ = 600-1,100)
Chapter 2: SSBANDING's Patented Oscillation Processing Workflow
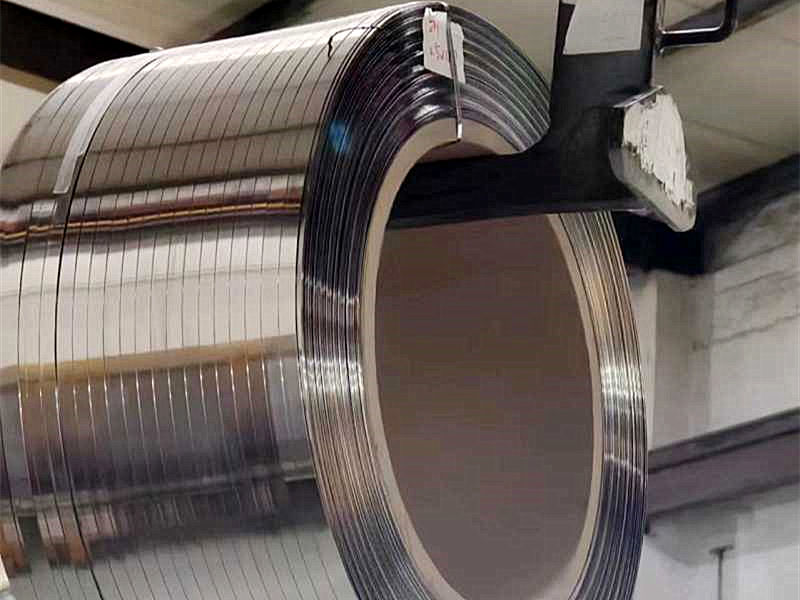
Step 1: Precision Cold Rolling
Using 4-high reversing mills, we achieve:
- Thickness tolerance: ±0.02mm (vs. ±0.05mm industry standard)
- Surface finishes: BA (bright annealed) or 2B (matte) per application needs
Step 2: Oscillation Slitting Technology
Core innovation differentiating oscillating bands from conventional strips
- Diamond-coated oscillating blades: 120 cycles/min dynamic cutting
- Burr-free edges: ≤5μm roughness (Ra) via tungsten carbide polishing
- Width range: 2.5mm to 50mm (±0.1mm precision)
Step 3: Seamless Multi-Strip Welding
- Laser-TIG hybrid welding: ≤0.1mm seam tolerance
- Red epoxy marking: 20cm weld-point identification for traceability
- X-ray inspection: 100% defect detection rate
Step 4: Eco-Conscious Packaging
- VCI paper wraps: Prevent corrosion during shipment
- Blockchain-tracked coils: Scan QR codes for full production history
Chapter 3: Technical Breakthroughs in Oscillation Processing
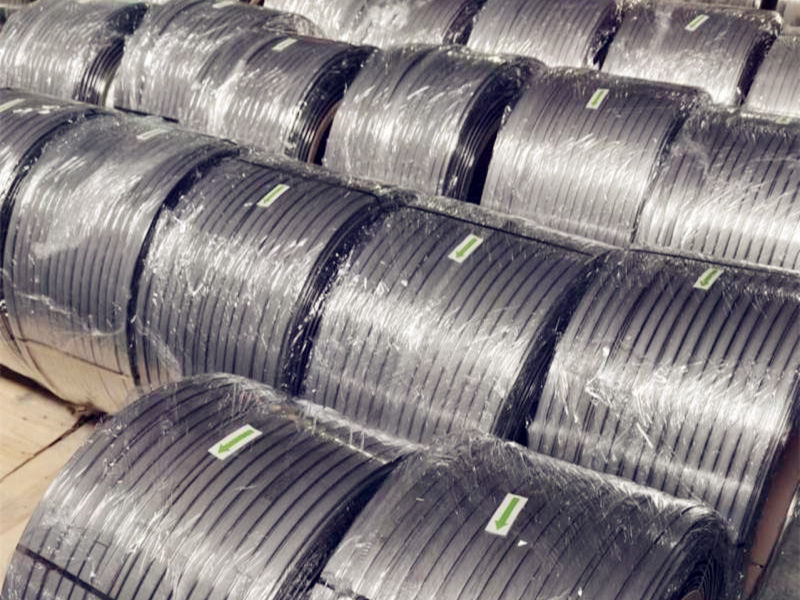
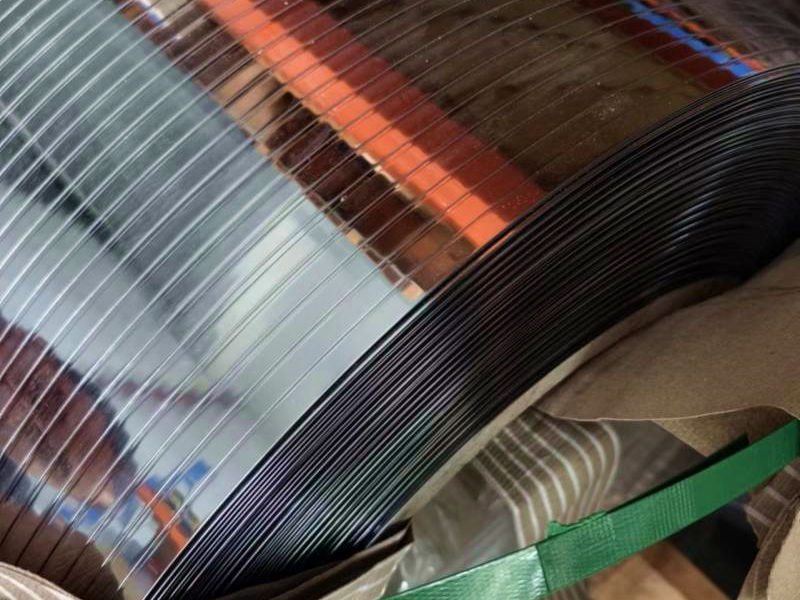
Oscillation vs. Conventional Slitting (Performance Comparison)
Parameter | Traditional Method | SSBANDING Oscillation | Improvement |
Cutting Speed | 50-80 m/min | 120-150 m/min | 85% ↑ |
Edge Burr Rate | 12-18% | 0.9% | 92% ↓ |
Material Yield | 91-94% | 99.2% | 8% ↑ |
Energy-Efficient Thermal Treatment
- Hydrogen bright annealing: 1050°C furnace with 15% energy recovery
- In-line hardness control: HV 200-250 via real-time cooling rate adjustment
Chapter 4: Industry-Specific Applications & Case Studies
Case 1: Automotive Exhaust System Assembly
- Magnetic feeding: Enables robotic handling without slippage
- High-temperature resistance: Withstands 800°C exhaust gases
Case 2: Smart Kitchen Appliance Manufacturing
- Mirror-finish BA surfaces: Ideal for dishwasher panels and oven linings
- FDA-compliant edges: Electropolished to Ra ≤0.4μm for food safety
Case 3: Cost-Sensitive Electronics Shielding
- EMI/RFI shielding: Magnetic properties block 85% interference
- Lightweight coils: 13kg-1,000kg customizable weights
Chapter 5: SSBANDING's Competitive Edge
Vertical Integration: Control from chromium alloy smelting to final packaging
R&D Focus: 7 patents in oscillation processing and welding
Sustainability: 98% scrap recycling rate via closed-loop systems
Conclusion: The Oscillation Revolution in Ferritic Steel
SSBANDING’s 430 stainless steel oscillating bands redefine automated production economics. By merging chromium’s innate corrosion resistance with oscillation-driven efficiency, we empower manufacturers to achieve:
- 20% lower TCO vs. 304-grade alternatives
- Zero unplanned downtime via AI-powered defect prevention
- Carbon-neutral compliance through lean manufacturing
Request free samples to experience how our oscillating bands can optimize your production flow.
Tags
- 430 stainless steel oscillating band supplier
- Ferritic stainless steel coils
- Chromium-rich magnetic steel strip
- Burr-free edge processing technology
- Automated production line solutions
- Cost-effective stainless steel bands
- High-temperature resistant oscillating coils