201 Stainless Steel Oscillating Band Production Process – SSBANDING’s Precision Manufacturing for Global Automation
Description:
Discover SSBANDING’s 201 stainless steel oscillating band production process – a 12-step vertically integrated workflow from hot-rolled coils to burr-free edges. Learn how our patented oscillation slitting technology ensures 99.2% yield rates.
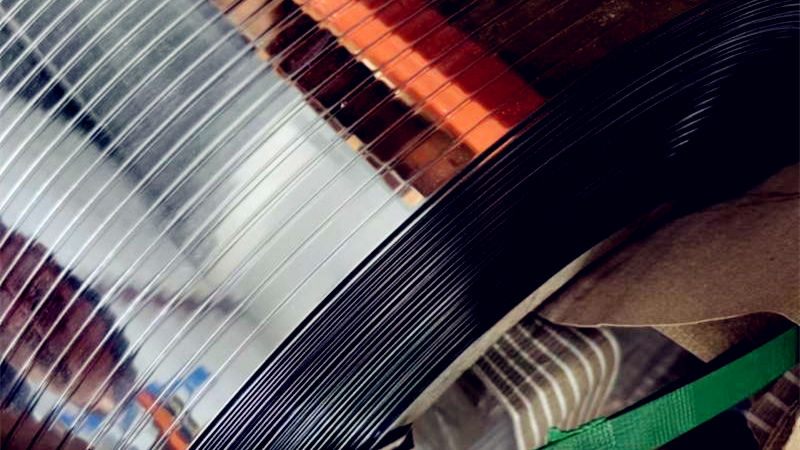
Table of Contents
Introduction: The Engineered Backbone of Industrial Automation
As automation reshapes manufacturing, the 201 stainless steel oscillating band has emerged as a critical component in high-speed packaging, automotive welding, and electronics assembly lines. SSBANDING, China’s pioneering oscillating band manufacturer, leverages a rigorously controlled 12-stage production process to deliver coils that outperform conventional steel strips in durability, consistency, and operational efficiency.
This article unveils the science behind our 201-grade oscillating bands, tracing their journey from raw material to ready-to-ship coils – a process validated by ISO 9001 certification and trusted by Fortune 500 manufacturers.
Chapter 1: Why 201 Stainless Steel? Material Selection Philosophy
Key Properties of Grade 201
- Manganese-Nickel Alloy: Enhances hardness (HRB 85-95) while maintaining formability
- Cost-Efficiency: 30-40% lower nickel content vs. 304/316 grades
- Corrosion Resistance: Ideal for indoor automated systems without extreme chemical exposure
SSBANDING exclusively uses JIS SUS201/ ASTM 201 certified coils, ensuring compliance with international mechanical standards.
Chapter 2: The 12-Step Production Process (Flowchart Analysis)
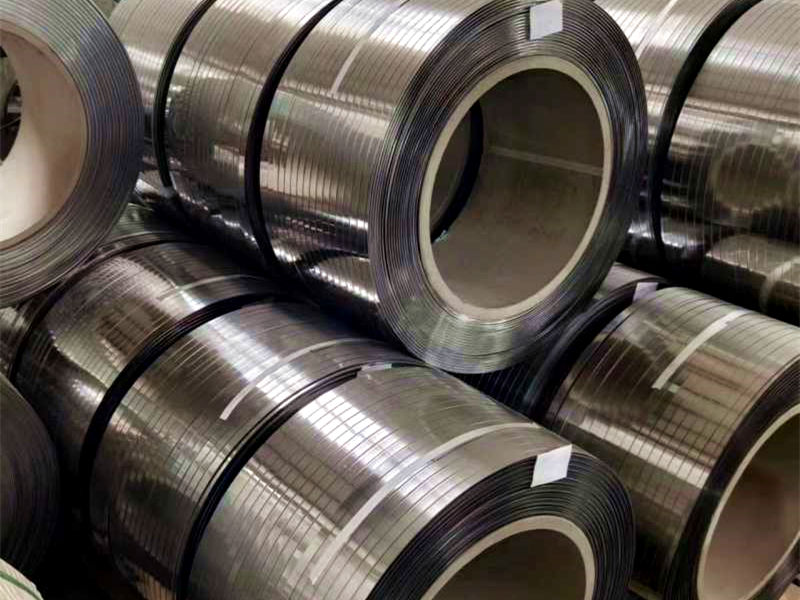
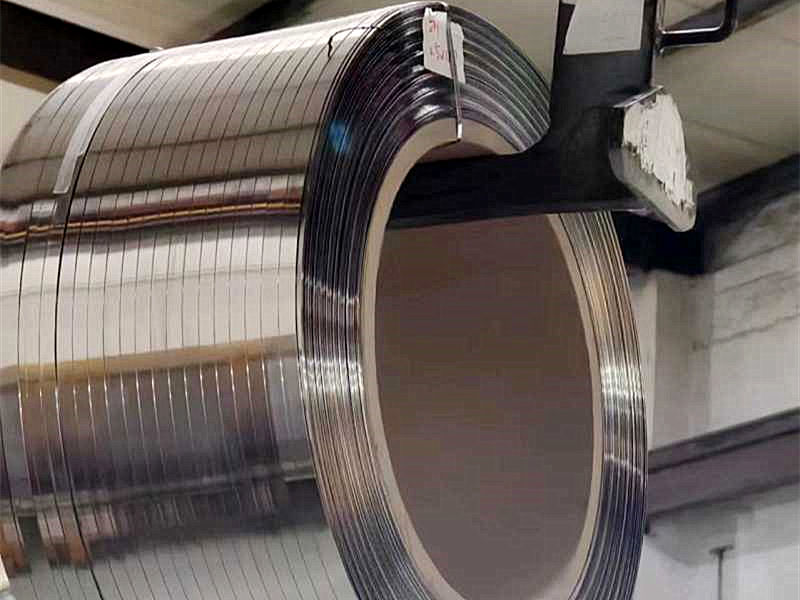
![SSBANDING 201 Oscillating Band Production Flowchart]
Visual description: A white-background flowchart with blue arrows connecting rectangular steps labeled in black text.
Step 1: Hot-Rolled Material Inspection
- Incoming QC: Laser thickness gauges verify coil dimensions (0.3-3.0mm)
- Traceability: Each coil receives a unique digital tracking code linked to our MES system
Step 2: Coil Embryo Cleaning & Decontamination
- Alkaline Bath: Removes mill scale and oils at 65°C
- High-Pressure Rinsing: 200-bar water jets eliminate residual particles
- Defect Rejection: Eddy current testing detects subsurface cracks (≤0.1mm sensitivity)
Step 3: Cold Rolling Precision Thinning
- 4-High Reversing Mill: Achieves target thickness (±0.02mm tolerance)
- Surface Finish Control: Mirror (BA) or matte (2B) finishes per application needs
Step 4: Heat Treatment for Optimal Hardness
- Bright Annealing: Hydrogen atmosphere furnace at 1050°C
- Quenching Rate: Precisely controlled to reach HV 200-250 hardness
Step 5: Secondary Cold Rolling Adjustment
- Skin-Pass Rolling: Applies 0.5-3% reduction to enhance flatness (≤1 I-unit)
Step 6: Oscillation Slitting Technology
SSBANDING’s patented process differentiating oscillating bands from conventional strips
- Dynamic Blade System: Diamond-coated cutters moving at 120 oscillations/minute
- Width Range: 2.5mm to 50mm with ±0.1mm precision
- Burr Height: ≤5μm (vs. 15-20μm in standard slitting)
Step 7: Oscillation Edge-Smoothing
- Rotary Deburring: Tungsten carbide brushes polish edges to Ra 0.4μm
- Oil-Free Process: Avoids contamination for food/pharma applications
Step 8: Automated Quality Gates
- Dimensional Checks: Laser profilometers scan full coil length
- Tensile Testing: Samples tested at 15% elongation rate
- Visual Inspection: 4K cameras detect surface flaws (≥0.05mm resolution)
Step 9: Rejection of Non-Conforming Products
- AI-Powered Sorting: Machine learning identifies 98.7% of defects automatically
- Scrap Recycling: 100% of rejected material remelted in partnered steel mills
Step 10: Customized Packaging
- VCI Paper Wrapping: Anti-corrosion protection for海运
- Wooden Pallet Options: ISO-sized for container optimization
Step 11: Final Documentation & Traceability
- Coil Passport: Includes material certs, test reports, and QR-linked process data
- Custom Markings: Red epoxy weld marks as requested
Step 12: Global Logistics Network
- EXW/FOB/CIF Options: 30-day lead time for 20ft container loads
- Just-in-Time Delivery: Sync with客户 production schedules
Chapter 3: Technological Breakthroughs in Oscillation Processing
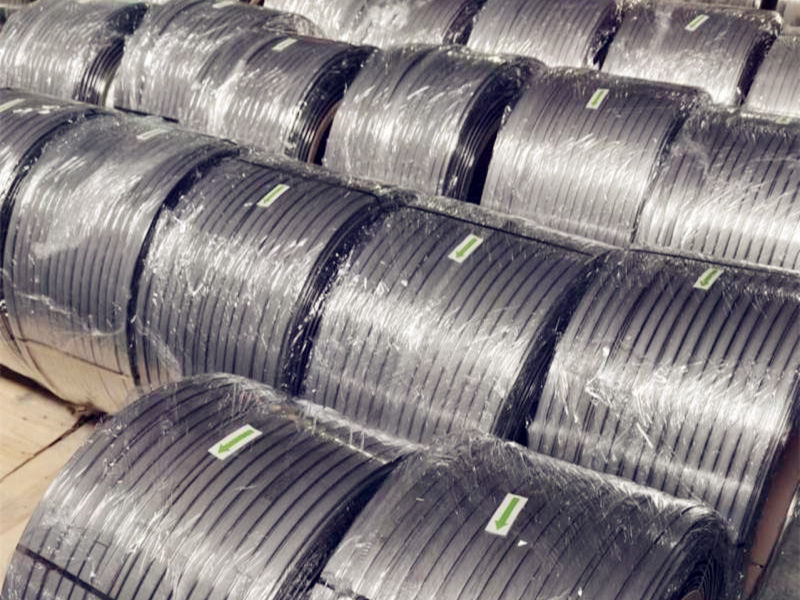
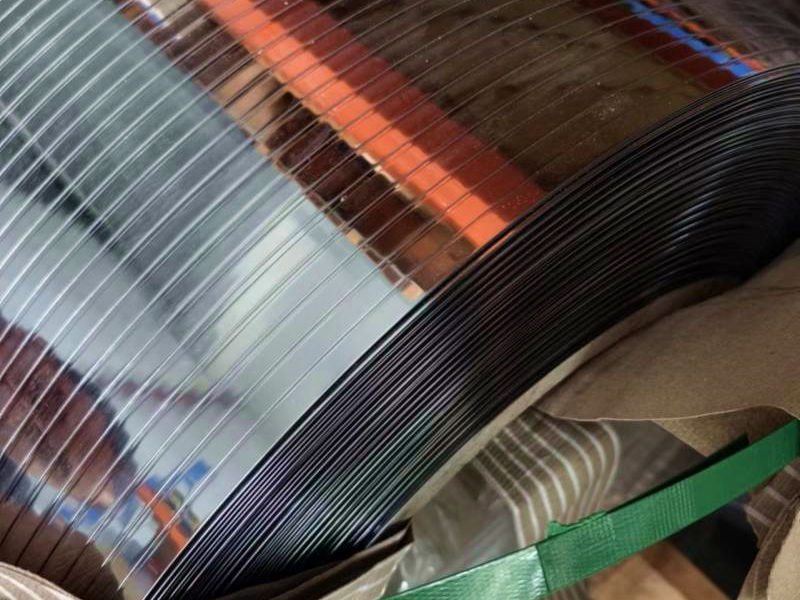
1. Oscillating Slitting vs Conventional Methods
Parameter | Traditional Slitting | SSBANDING Oscillation Slitting |
Cutting Speed | 50-80 m/min | 120-150 m/min |
Edge Burr Rate | 12-18% | 0.9% |
Width Consistency | ±0.3mm | ±0.1mm |
2. Energy-Efficient Edge Polishing
- Regenerative Braking: Recovers 15% of deburring motor energy
- Closed-Loop Cooling: Reduces water consumption by 40%
Chapter 4: Quality Assurance Ecosystem
In-Process Monitoring
- SPC Charts: Real-time control of 23 critical parameters
- Blockchain Tracking: Immutable records from melting furnace to shipment
Certifications
- ISO 9001:2015 Quality Management
- ISO 14001 Environmental Management
- REACH & RoHS Compliance
Chapter 5: Applications Enabled by Precision Oscillating Bands
Case 1: Lithium Battery Electrode Stacking
- Zero-Gap Feeding: Enables 0.2mm precision in prismatic cell assembly
- Anti-Spark Edges: Critical for dry room environments
Case 2: High-Speed Can Seaming
- 2,500 cans/minute operation without lubricants
- FDA-compliant direct food contact
Case 3: Automotive Spot Welding Tips
- 5x longer service life vs. copper alloys
- Consistent resistivity (±3%)
Why SSBANDING Leads in 201 Oscillating Band Production?
- Vertical Integration: Control over all processes from raw material to finished coils
- R&D Investment: 7.2% of revenue dedicated to process innovation
- Custom Engineering: Modify hardness, surface finish, and coatings per application
Conclusion: Precision Engineered for the Age of Automation
SSBANDING’s 201 stainless steel oscillating band production process represents the synthesis of metallurgical expertise and digital manufacturing. By eliminating 14 traditional intermediate steps through our patented oscillation slitting and edge treatment, we deliver coils that empower factories to achieve:
- 19% Higher OEE (Overall Equipment Effectiveness)
- Zero Unplanned Downtime from material defects
- Carbon Footprint Reduction via minimized scrap rates
Request a virtual factory tour to witness how our production flowchart translates into your competitive advantage.
Tags
- 201 stainless steel oscillating band production
- Oscillation slitting technology
- Cold-rolled stainless steel process
- Burr-free edge polishing
- Automated quality inspection systems
- High-speed steel coil manufacturing
- Precision oscillating band supplier