The Ultimate Guide to Stainless Steel Banding Materials: Exploring the Versatility of 200-Series Alloys
Unlocking the Power of 200-Series Stainless Steel for Industrial Excellence
As a leading stainless steel banding manufacturer, SSBANDING understands the critical role material selection plays in delivering durable, cost-effective solutions. This in-depth exploration focuses on the 200-series stainless steel alloys – a family of materials revolutionizing industries with their unique balance of strength, formability, and corrosion resistance.
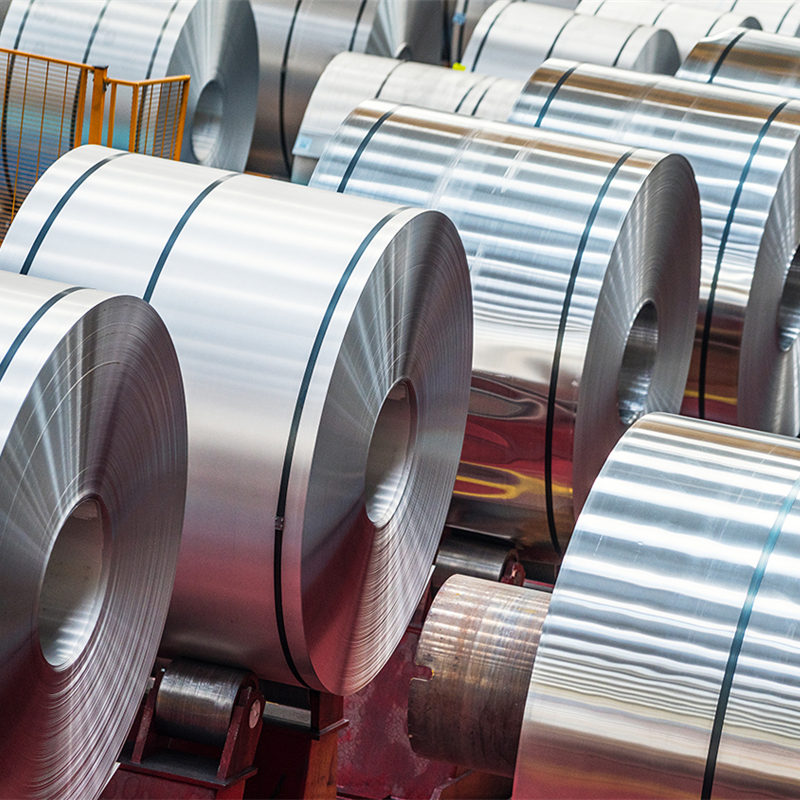
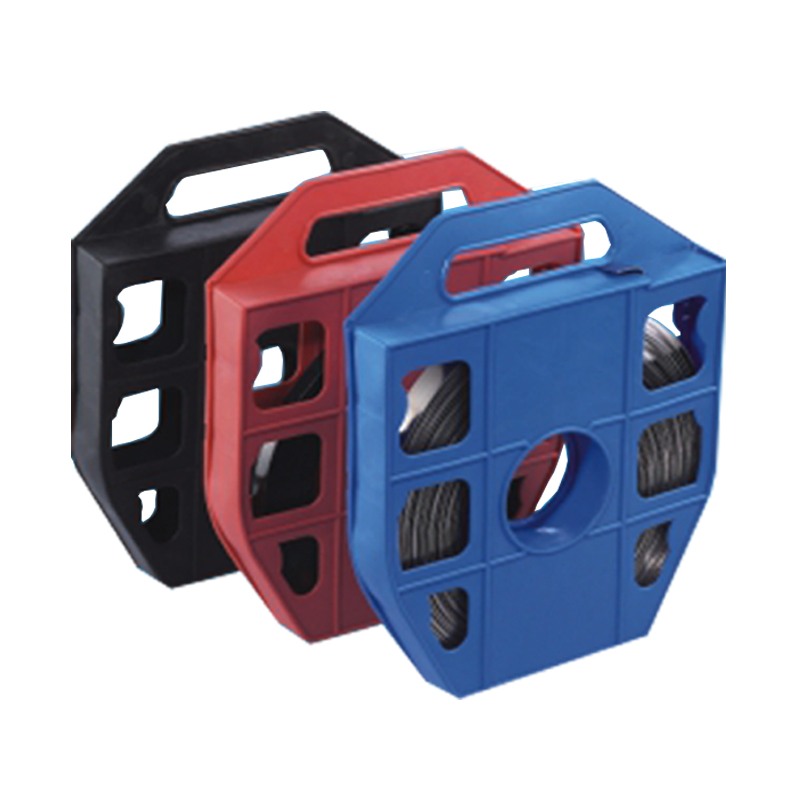
Table of Contents
Chapter 1: The Science Behind Stainless Steel Banding
1.1 What Makes Stainless Steel “Stainless”?
Stainless steel derives its corrosion resistance from a minimum 10.5% chromium content, which forms a self-repairing chromium oxide layer when exposed to oxygen. While chromium is the cornerstone element, modern metallurgy introduces nickel, manganese, and nitrogen to create specialized alloys tailored for specific applications.
1.2 Why 200-Series Dominates Banding Applications
The 200-series (Cr-Ni-Mn system) offers three critical advantages for industrial banding:
- Cost Efficiency: Reduced nickel content compared to 300-series
- Enhanced Strength: Manganese-induced work hardening
- Formability: Excellent cold-working characteristics
Chapter 2: Decoding 200-Series Alloy Chemistry
2.1 Core Composition Breakdown
Element | Role in 200-Series | Typical Content |
Chromium | Corrosion Resistance | 16-19% |
Nickel | Austenite Stability | 4-6% |
Manganese | Nitrogen Solubility | 5-15% |
Nitrogen | Strength Booster | 0.15-0.4% |
Data compiled from international standards
2.2 Key Alloy Variations in Banding Production
201 Stainless Steel
- Composition: Cr 17-19%, Ni 3.5-5.5%, Mn 5.5-7.5%
- Best For: Architectural banding, food service equipment
- SSBANDING Tip: Ideal for indoor applications with moderate corrosion exposure
202 Stainless Steel
- Composition: Cr 17-19%, Ni 4-6%, Mn 7.5-10%
- Mechanical Edge: Tensile strength up to 740 MPa after cold working
- Application Spotlight: Automotive trim fasteners, conveyor system components
204Cu Stainless Steel
- Innovation: Copper addition (2-4%) enhances deep-drawing capability
- SSBANDING Advantage: Reduces cracking risk in complex banding profiles
205 Stainless Steel
- High-Strength Formula: Mn 14-15.5%, N 0.32-0.4%
- Performance Benchmark: Yield strength surpasses 304 stainless by 25%
Chapter 3: Performance Comparison Across Steel Families
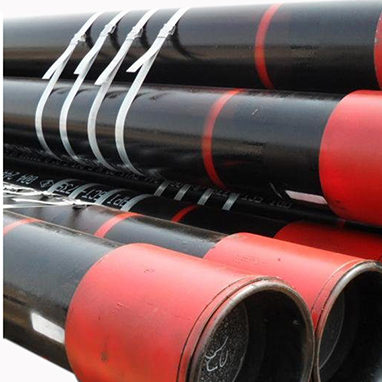
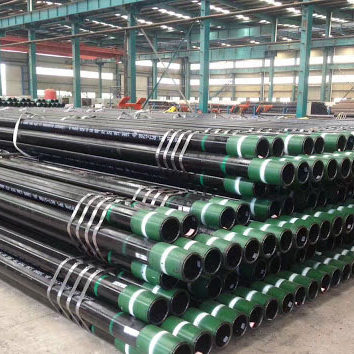
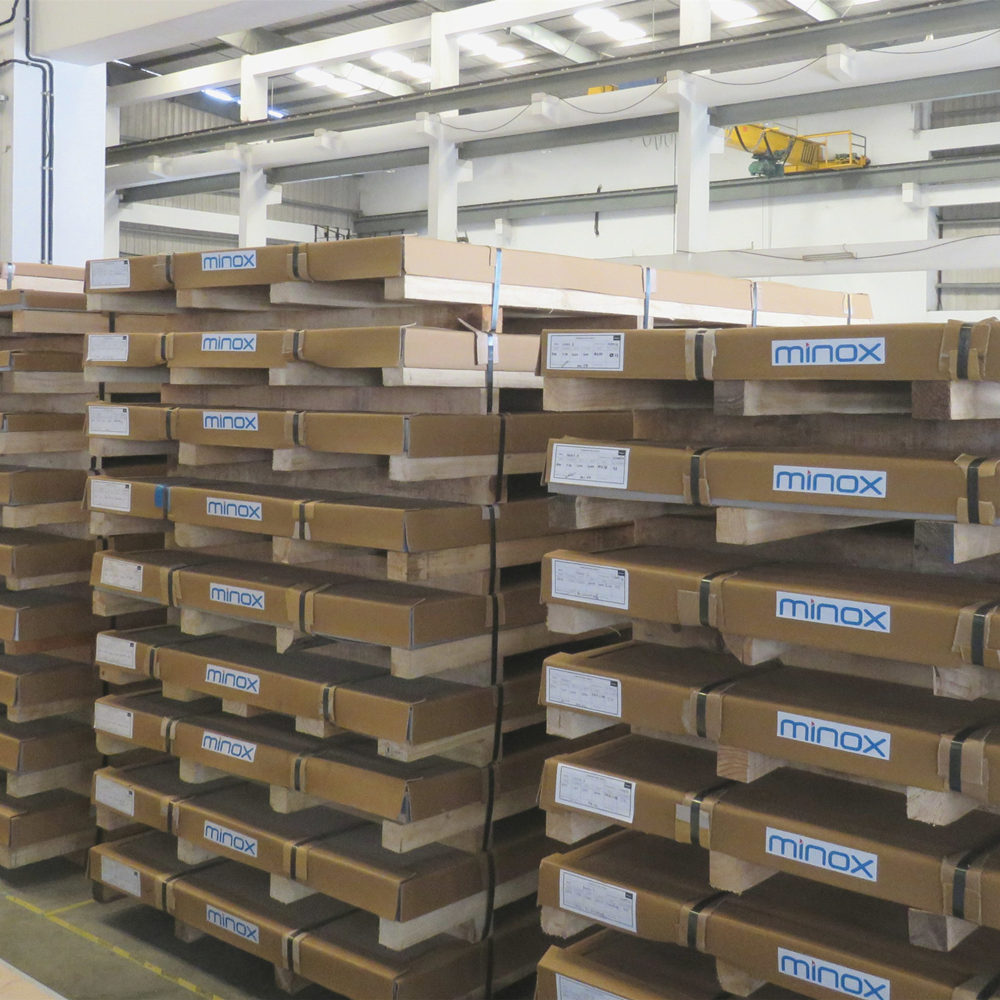
3.1 200 vs. 300 vs. 400 Series: The Banding Perspective
Property | 200-Series | 300-Series | 400-Series |
Corrosion Resistance | Moderate | Excellent | Poor |
Magnetic Response | Weak/Negligible | Non-magnetic | Strong |
Work Hardening | Significant | Moderate | Low |
Cost Index | 1.0 | 1.8-2.2 | 0.7-0.9 |
3.2 Overcoming 200-Series Limitations
- Surface Treatment: Passivation processes enhance corrosion resistance
- Annealing Protocols: Mitigate work hardening during deep drawing
- Alloy Blending: Strategic nitrogen addition improves pitting resistance
Chapter 4: Industrial Applications Redefined
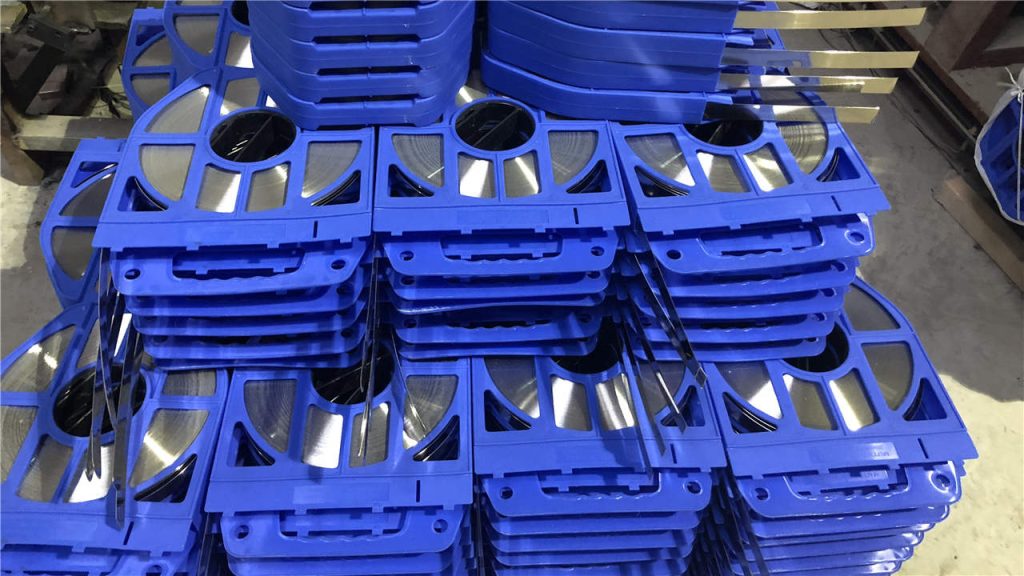
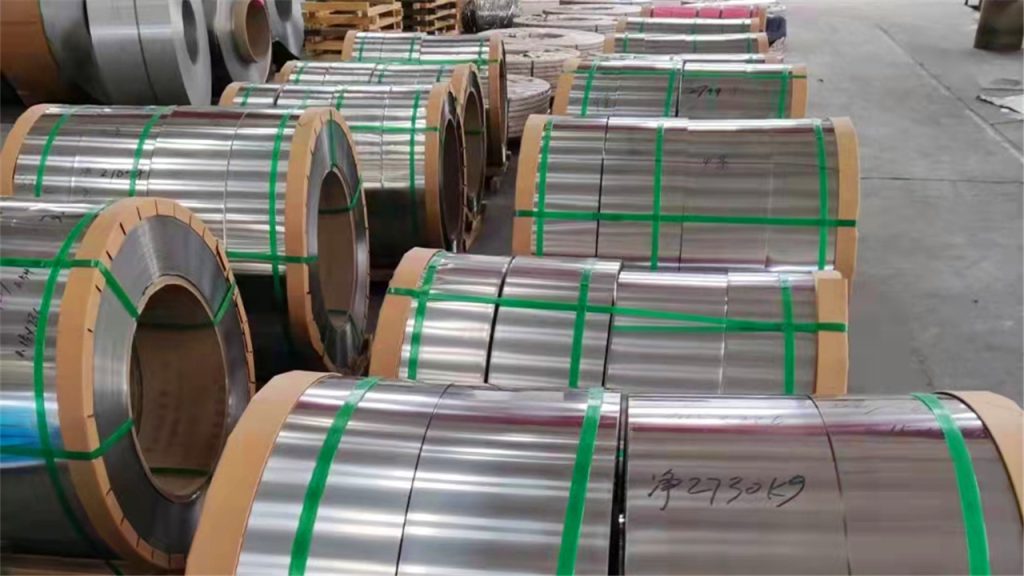
4.1 Revolutionizing Kitchen Equipment
- Case Study: Commercial oven banding using 201 alloy
- Benefit Profile: Withstands 800°F continuous operation while resisting grease corrosion
4.2 Automotive Innovation Drivers
- Application: EV battery containment systems (216 alloy)
- Material Advantage: Mo-enhanced (2-3%) version resists road salt degradation
4.3 Construction Breakthroughs
- Project Example: Seismic-resistant building ties using 205 grade
- Performance Metric: 40% higher vibration damping vs. carbon steel alternatives
Chapter 5: SSBANDING's Material Expertise
5.1 Our 200-Series Product Matrix
Grade | Thickness Range | Surface Finish Options | Special Features |
201 | 0.1-3.0mm | 2B, BA, Hairline | Economical general-purpose |
202 | 0.2-4.5mm | Embossed, Colored | High-visibility applications |
204Cu | 0.15-2.5mm | Mirror Polish | Superior formability |
205 | 0.3-6.0mm | Brushed | Structural reinforcement |
5.2 Customization Capabilities
- Precision Slitting: ±0.05mm tolerance for critical applications
- Surface Engineering: PVD coating options for enhanced wear resistance
- Certification Support: ASTM A666, EN 10088-2, JIS G4305 compliance
Chapter 6: Future Trends in Banding Materials
6.1 Smart Alloy Development
- Self-Healing Coatings: Micro-encapsulated corrosion inhibitors
- Hybrid Composites: Graphene-reinforced 200-series variants
6.2 Sustainability Initiatives
- Closed-Loop Recycling: 98% material recovery rate in production
- Low-Carbon Alloys: Hydrogen-based reduction metallurgy
Why Choose SSBANDING's 200-Series Solutions?
Our technical team has pioneered three critical advancements in stainless steel banding:
- Stress-Relief Edge Treatment – Eliminates micro-cracking in high-stress areas
- Proprietary Annealing Process – Achieves HRB 85 hardness without brittleness
- Custom Alloy Development – Site-specific corrosion resistance formulations
With over 200 metallurgical combinations and 15+ surface finish options, SSBANDING delivers precision-engineered banding solutions for every industrial challenge. Contact our material specialists today to optimize your next project with 200-series excellence.